AOG Details
Aircraft type: Business Jet
Location: Jordan
Time of Report: 13:00
System Affected: Hydraulic System #3
Total Downtime: Approximately 36 hours
Brief Summary
This AOG case involved an aircraft grounded in Jordan due to an out of limits hydraulic leak on System #3. A local engineer traced the issue to a pipe connected to the manifold via a permaswage fitting.
As a precaution, the replacement pipe was ordered from Chicago immediately upon confirmation of team deployment. An onboard carry was arranged to ensure rapid delivery. The attending team completed the installation overnight, returning the aircraft to service by 02:00 the following morning.
Initial Assessment
At 13:00 local time, technical support was requested for an aircraft grounded at an airport in Jordan. The issue was a visible leak within Hydraulic System #3, reportedly emanating from the manifold area. A local engineer conducted an initial inspection and identified the likely cause as a leak at a permaswage fitting attached to a hydraulic pipe on the #3 manifold.
Hydraulic System #3 is essential for primary control surfaces, landing gear, and brakes. Even a minor leak from a high-pressure fitting necessitates immediate attention and renders the aircraft unserviceable until resolved.
Diagnostic Approach
With a likely component identified, the support team confirmed mobilisation. The replacement pipe was proactively ordered from a supplier in Chicago as a precautionary measure to avoid delays pending further inspection.
Upon arrival in Jordan the following morning, the team inspected the system to verify the earlier diagnosis. Torque checks on the unions confirmed that the pipe was correctly secured, yet hydraulic fluid was clearly leaking at the swaging. The leak was definitive, and no further diagnostic steps were deemed necessary.
Given the system's function and the nature of the fitting, repairs were never under consideration. A full replacement was the only acceptable course of action to ensure system integrity and airworthiness.
Communication and Planning
With the component sourced in Chicago and the urgency of the situation clear, an onboard carry solution was initiated. A logistics specialist was assigned to collect the pipe in person and fly it directly to Jordan, eliminating the delays associated with conventional freight forwarding.
Meanwhile, the repair team boarded a flight from London Heathrow at 18:30 on the same day the support request was received. Their early arrival in Jordan enabled them to prepare the worksite and complete all preliminary checks ahead of the part’s arrival.
The operator leveraged an established relationship with local customs authorities to ensure expedited clearance for the incoming component.
Logistics and Installation
The onboard courier arrived in Jordan the following evening, and the replacement pipe was in hand by 22:30 thanks to fast-tracked customs clearance.
Well rested and prepared, the engineering team began the replacement immediately. The faulty pipe was removed, and the surrounding manifold area cleaned and inspected. The new pipe was installed and torqued to specification in accordance with the maintenance procedures.
The #3 hydraulic system was then bled to remove air and ensure proper pressure throughout. As only the pipe and associated fittings were disturbed, there was no requirement to cycle the landing gear, thanks to the aircraft’s well-designed hydraulic system architecture. This isolation of subsystems allowed for a quicker, more targeted post-repair process.
With installation complete and all checks passed, documentation was finalised and the release to service signed by 02:00.
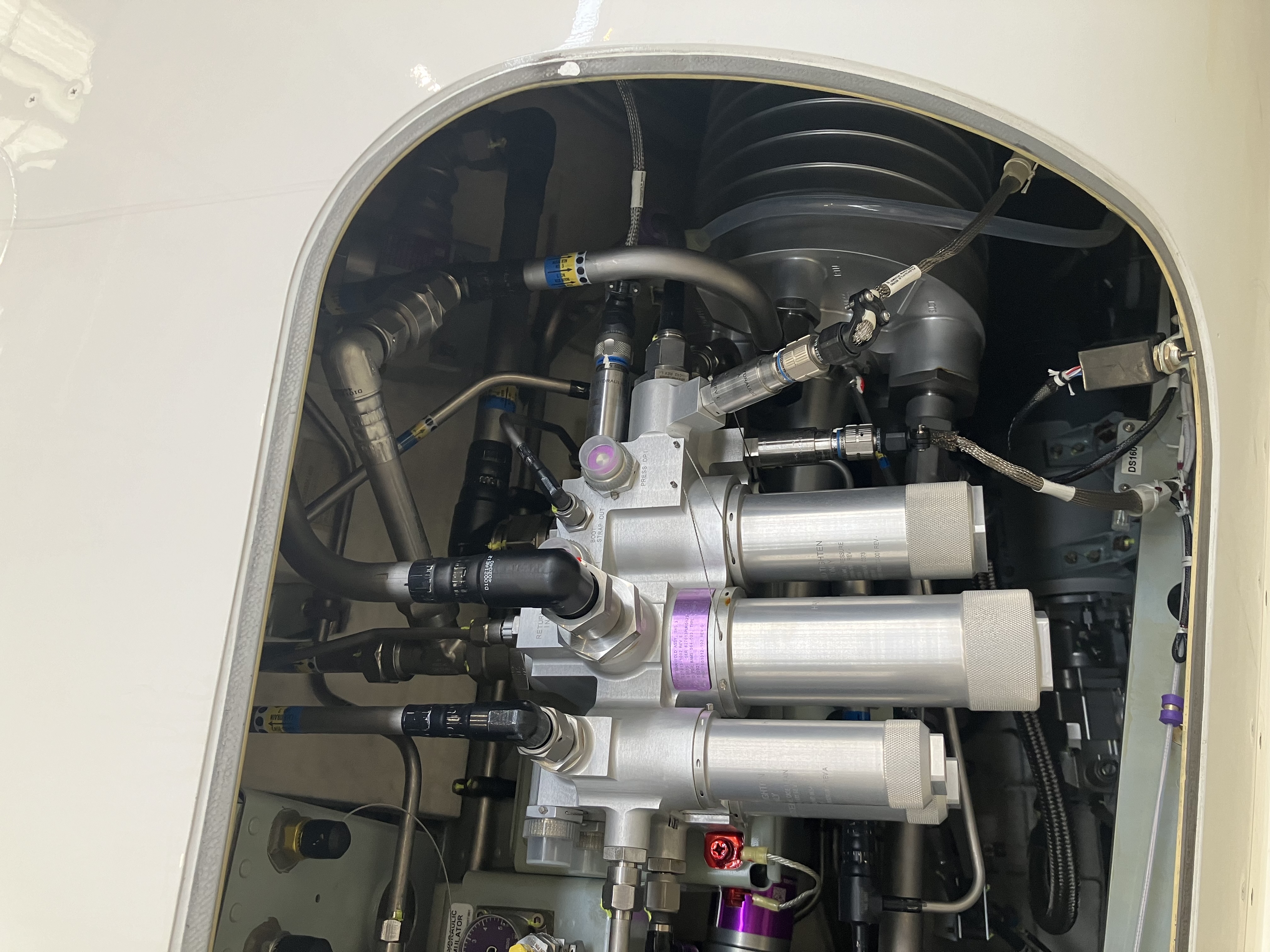
Testing and Return to Service
Following completion of the work, the hydraulic system was pressurised and tested. System readings were checked both locally and via cockpit indications. There were no further signs of leakage, and the system held pressure throughout the observation period.
This particular aircraft's modular hydraulic design proved highly advantageous, enabling efficient bleeding and system verification without the need for full gear swings or complete system cycling. This not only reduced the time to return the aircraft to service but also eliminated the significant logistical challenges typically involved in jacking an aircraft at a remote location, where ground support equipment, jacking points, or weight-on-wheels simulations may be difficult to access.
The attending team departed Jordan later that day, having completed the recovery in just under 36 hours from the time of first contact.
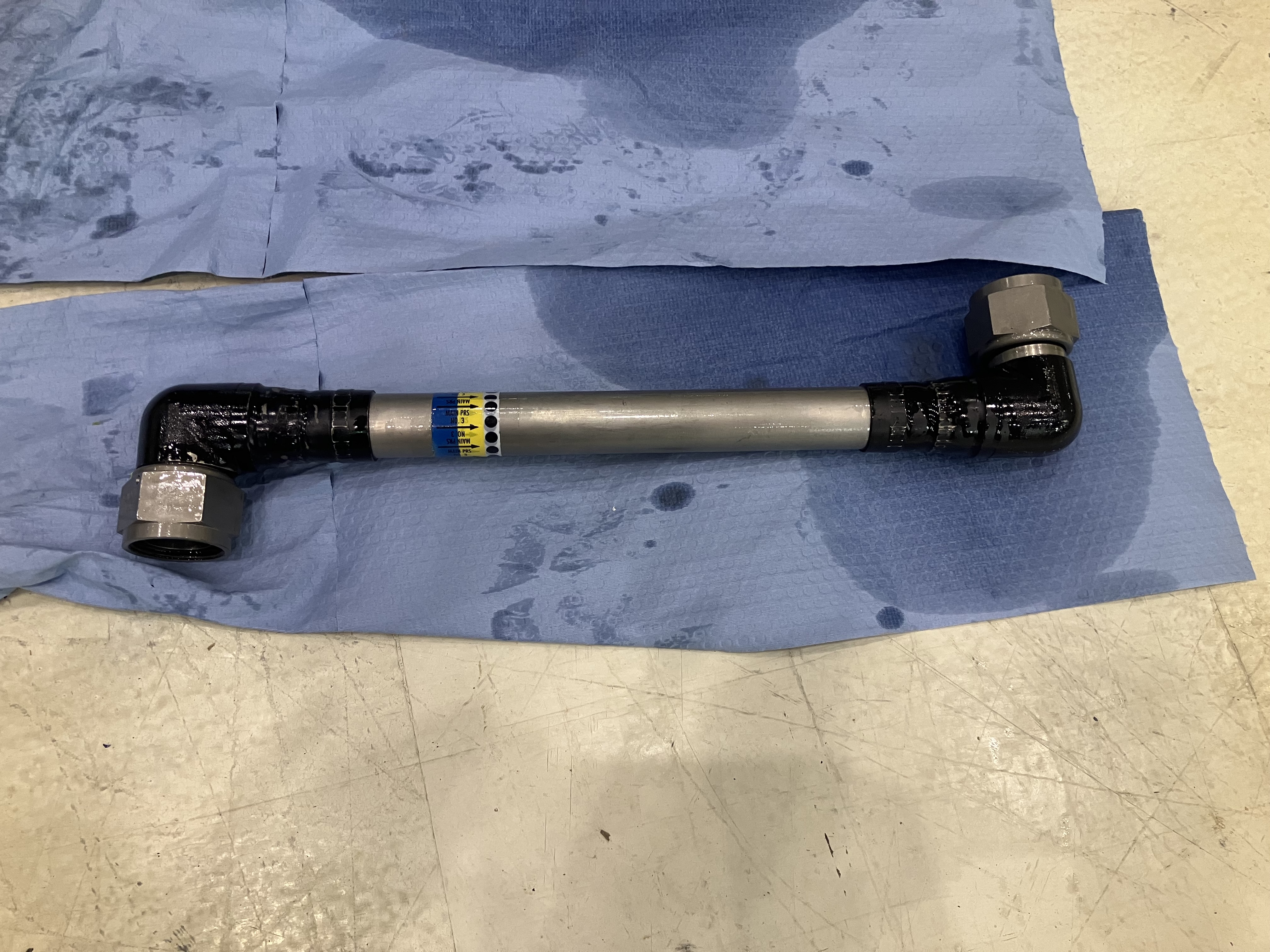
Technical Reflection
This recovery highlights the value of forward planning and decisive action in minimising downtime. The decision to proactively order the replacement pipe before on-site confirmation was a key factor in the success of this operation. So too was the use of an onboard carry, which eliminated potential delays and kept the timeline tight.
From a technical standpoint, this case reinforces the importance of field experience in accurately interpreting symptoms and trusting initial assessments. Although the fitting was torqued correctly, it had still failed, which serves as a reminder that mechanical integrity can degrade even without installation error.
Finally, the aircraft's design contributed meaningfully to the smooth recovery. The ability to isolate hydraulic subsystems and avoid unnecessary cycling significantly reduced the workload and complexity of the repair. Overall, this was a textbook example of coordinated logistics, sound engineering judgement, and well-executed planning in the field.
If you find yourself heading to Jordan, avoid the Amman Airport Hotel. It might seem like a convenient stop near Queen Alia Airport, but the rooms are worn, the hygiene is questionable, and yes, there were cockroaches. After a long AOG shift, it’s the last place you want to try and get some rest.